Materials of Progress: Steel and European Narratives of Civilisation
- EPOCH
- Mar 1
- 7 min read
Anaïs Walsdorf | University of Warwick

The process started quietly. For the first ten minutes, hot gases rose from the towering converter, small orange sparks alighted here and there – it was nothing Henry Bessemer hadn’t seen before. But the experiment had only just begun. Inside, the hot air blast was rising rapidly to a scalding 1,650° C. All at once, oxygen and carbon collided, sending up an enormous white hot flame. As the stream of sparks grew, a series of small explosions thundered, shooting red molten metal into the air. The apparatus had become a veritable volcano in a state of active eruption. In fact, the machine roared with temperatures twice that of an earthly volcano. The engineers, fearing that laboratory materials would set aflame, scrambled to turn off the raging machine – but it was too hot to approach. Finally, within ten more minutes, the flames had ceased, and the process was complete. Henry Bessemer poured th, the flames had ceased within ten more minutes e blistering hot steel into a pan, letting it cool into a solid ingot. He realised in awe that the tempestuous machine had converted crude iron into steel.
For most of human history, charcoal, or slow-burnt wood, had been the world’s primary source of fuel. By the eighteenth century, Britain was in the midst of a shortage of timber after centuries of deforestation. In 1709, British ironmaster Abraham Darby first fueled his ironworks furnace with coal in the village of Coalbrookdale, England. Compared to charcoal, he found that coke, a carbon-rich form of coal, produced higher temperature levels and the power to support larger furnaces. A century and a half later, coke provided the power that Bessemer’s converter needed to create the first industrial process that could inexpensively mass produce steel, turning it into a true industrial material.
From 1838 to 1883, engineer and inventor Henry Bessemer patented at least 129 inventions related to iron, steel, and glass technologies. However, his most influential contribution to industrializing Britain was the Bessemer converter. Inspired by the brutal Crimean War, Bessemer aimed to craft a gun metal that could support heavier projectiles for artillery guns. When he began his experiments in the early 1850s, the most popular iron-based manufacturing materials were cast iron and wrought iron. While cast iron has high tensile strength, or ability to endure stress without fracturing – such as the explosion of a firearm – it was too hard and brittle to withstand the firepower Bessemer dreamt of. Wrought iron is soft and pliable, however it lacks tensile strength. Bessemer found that the unique characteristics of steel, defined as an alloy of iron and 0.5-1.5% of carbon, allow it to be both pliable and strong – a material that would enable the development of technology and infrastructure that was beyond iron’s material capacity. While steel had been known to humans since antiquity, the significance of Bessemer’s process was in his choice of fuel – ‘an absolutely necessary condition of success’, he concluded, was ‘the rapidity of action, ending in a violent eruption’.

Upon witnessing the birth of steel through the ‘eruption of cinder, and the accompanying huge body of flame’ of Bessemer’s process, a group of visiting investors ‘themselves were converted’. In 1856, Bessemer patented his process. Throughout the second half of the nineteenth century, steel production rose exponentially as a rapid succession of improvements to the process followed. In 1886, the ‘father of English metallurgy’ John Percy proclaimed that ‘the day of steel has arrived… steel is destined to exercise an important influence on the destinies of the human race.’ The booming steel industry boosted the efficiency, capacity, and scale of British manufacturing power, ushering in what has been termed the Second Industrial Revolution. Development in steel technologies also strengthened British imperial expansion. British military power by land and sea embraced steel.  Powerful steel guns intensified the scale of colonial violence, while steel railways, warships, and bridges facilitated expansion, extraction, and the transportation of commodities. Indeed, railways remain evergreen symbols of British imperialism from South Asia to East Africa. Steel quickly became the symbolic and narrative material of European progress.
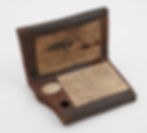
Racialised narratives surrounding the use of metals were already circulating by the time steel became an important material. In 1849, archaeologist Jens Worsaae wrote on the transition from the Stone Age to the Bronze Age, writing that ‘then… came races who possessed metals, and some degree of civilisation’. One President of the Ethnological Society of London, John Lubbock, dismissed what he saw as the ‘non-metallic savages’ of Australia, the Pacific Islands, South Africa, and the Americas.  The productive burning power of Bessemer’s converter added to racialised narratives around metallurgical technology and civilisational progress. In his 1886 Presidential Address to the British Iron and Steel Institute, John Percy asserted that:
It is interesting, moreover, to trace the history of the metallurgic art, and to note how the rude and laborious processes of former times have gradually acquired the marvellous development which we observe in Europe at the present day. In order to form a vivid conception of this progress, we have only to witness the Hindoos [sic] toiling laboriously at their bellows made of skin, to extract a few pounds of iron from their little furnace, scarcely larger than a chimney-pot, and then to direct our attention to the gigantic blast-furnace of modern times, urged by a blast-engine, requiring for its movement the equivalent in steam-power of a hundred horses, and yielding upwards of two hundred tons of iron a week.
Such civilisational narratives about steel served to dehumanise non-European populations and justify colonial expansion and violence. In 1867, John Percy answered an inquiry from the Secretary of State on behalf of the India Public Works Department about using the Bessemer process in the manufacture of railways in India. In addition to being the foremost metallurgist in Britain, Percy had been a close advisor to Henry Bessemer as he developed his process. Percy advised the colonial Indian government that it was indeed desirable to attempt to ‘instruct them in the greatly advanced state of the art of smelting and manufacturing iron in Europe.’ The first railways that ploughed through the Indian countryside with steam-raising brute force served to facilitate the colonial extraction and circulation of colonial commodities, namely coal. In 1855, an early railway line connected Raniganj Coalfield to Calcutta, a centre of coal consumption. Industrial mining began in Raniganj in 1774, replacing dense forests and displacing Indigenous Bauri and Adivasi communities who relied on them. Men, women, and children were brought from all over the country to work the mine for long hours in dangerous conditions, making Raniganj the largest producer of Indian coal in the nineteenth century. By the 1880s, Raniganj was connected by steel rails to India and other British colonies, the combustion of coal on a large scale lowered the cost and labour involved in both the production of steel and in fuelling steam power that drove steel machines.
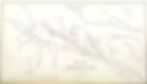
In the nineteenth century, steel became the physical and symbolic material of European technological superiority and industrial imperialism. As of 2024, the steel industry remains fossil-fuelled and is one of the most energy-intensive in the world, responsible for an estimated 10% of all greenhouse gas emissions. As global pressure to switch to sustainable energy and manufacturing practices rises, formally colonised countries continue to bear the brunt of new symbolic materials of progress, with rich nations and corporations reproducing narratives regarding the importance of bringing in their own expertise, technology, and finance to support– and profit from– the energy transition, echoing John Percy’s nineteenth-century ideas. For example, lithium has been dubbed the ‘white gold’ of the energy transition. Used in batteries for electric vehicles and to store solar and wind energy, global demand for lithium is expected to increase three-and-half-fold between 2023 and 2030. It is as important as ever to pay attention to how power affects which materials are used, and in what way. A quarter of the world’s lithium currently comes from Chile, where lithium production uses around 21 million litres of water per day, creating water-related conflicts in local communities that struggle to access clean water sources. The two companies in charge of lithium production in the country are U.S. firm Albemarle and SQM, a Chilean firm whose second-largest shareholder is a private Chinese firm, Tianqi. While lithium and other ‘green’ metals have been put forward as new heroes of progress and the energy transition, the political and economic structures that uphold the extraction and processing of these metals remain deeply unequal and destructive to the environment and communities at sites of extraction. It is not metals that have ‘[exercised] an important influence on the destinies of the human race’, but the capitalist and imperialist structures of power that control the extraction, production, and use of them. But this quote can also be read in hope- it is people with materials in their hands that have shaped the past, but it is also people with materials in their hands that will shape the future.Â
Further Reading:Â
Priya Satia, Empire of Guns: The Violent Making of the Industrial Revolution, (Stanford: Stanford University Press, 2018).Â
Clarence B. Davis, Kenneth E. Wilburn Jr, and Ronald E. Robinson (eds.), Railway Imperialism (New York: Greenwood Press, 1991)Â
Daniel R. Headrick, Power over peoples: technology, environments, and Western imperialism, 1400 to the present, (Princeton: Princeton University Press, 2010)Â
Glenn Adamson and Natalie E. Wright (eds.), Material Intelligence: Steel, (Milwaukee: Chipstone Foundation, 2024) (Available online at materialintelligencemag.org)Â
Jenny Bulstrode, ‘Black metallurgists and the making of the industrial revolution’, History and Technology, 39 (2023), 1–41.Â
Anaïs Walsdorf is an AHRC funded Collaborative Doctoral Partnership PhD researcher  working between the History department at the University of Warwick and the Science Museum in London. Her thesis explores the colonial institutions, systems and networks behind the 19th century mineralogical collection of metallurgist John Percy. Her research interests include histories of empire, mineralogy, extraction, and museums and collecting. Anaïs has a BA in Development Studies from UC Berkeley and a MSc in Empires, Colonialism and Globalisation from the LSE. Prior to beginning her PhD, she worked as a museum, library, and archive professional with institutions including the 1947 Partition Archive, Wellcome Collection and Library, the Migration Museum London, and the International Coalition of Sites of Conscience (ICSC).
Twitter: @global_subterraÂ